Introduction
Corrugated boxes are the backbone of modern-day packaging, used across industries for their durability, versatility, and eco-friendliness. From protecting fragile goods in transit to serving as a promotional tool for businesses, these boxes are a necessity now. So, what exactly are corrugated boxes, and how did they come about? This article is an exhaustive guide to their history, material, types, applications, advantages, environmental impact, and future perspectives, supported by facts and figures.
1. What are Corrugated Boxes?
Corrugated boxes are made up of corrugated fiberboard, which is a material made up of a fluted corrugated sheet (the “medium”) sandwiched by one or two flat linerboards. This form provides strength, resilience, and cushioning, which are ideal for packaging.
2. Historical Background
Origins: The corrugated material was patented in 1856 by Edward G. Healy and Edward E. Allen patented a method of pleating paper to give it a wavy appearance. The purpose of introducing this paper inside top hats was to make them more durable and comfortable to wear. In 1871, Albert Jones of New York and was then used to cover glass lantern chimneys and bottles. Oliver Long, however, made the design improved by adding a liner on one side of the fluted paper to create the single-face corrugated board in 1874.
Development: Pre-cut corrugated box, which revolutionized the packaging world, was created by Robert Gair in 1890. Corrugated boxes became universal by the beginning of the 20th century, used to ship and store goods, in place of boxes and wood crates.
Modern Era: Corrugated boxes are today a multi-billion-dollar industry, and advancing manufacturing technology and environmentally responsible innovations are propelling their growth.
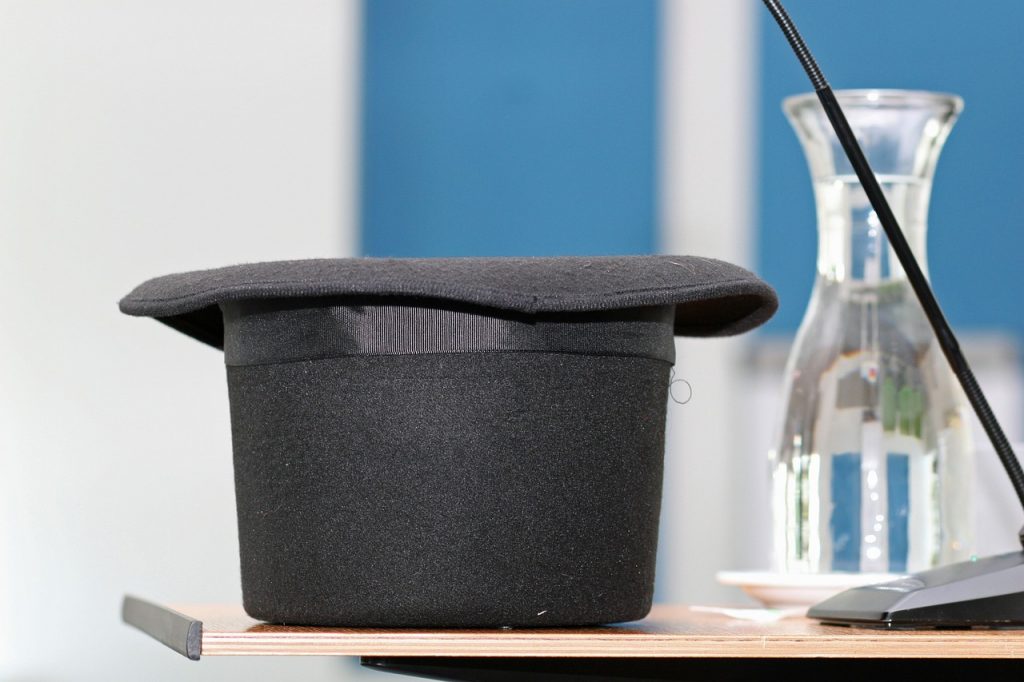
3. Structure of Corrugated Boxes
The corrugated box structure underlies their performance. Here it is, broken down:
Linerboard (Face Paper)
The linerboard is the flat sheet of the corrugated board. The most commonly used papers for the liner are kraft paper and test paper. A corrugated board’s inner liner is usually made from test paper, whereas its outer liner is made from kraft paper. Kraft paper is more expensive than test paper, but it is of higher quality. Kraft paper is primarily made from virgin chemical pulp fibers derived from wood and can be processed to have a variety of colors and textures. Additionally, it has a flatter surface, which makes printing easier. Furthermore, kraft paper is more resistant to tearing and bursting than test paper, thus providing better protection for goods. It is of various types, each having certain characteristics:
Type of Linerboard | Description | Common Uses |
---|---|---|
Kraft Liner | Made from virgin wood pulp, high strength | Heavy-duty packaging, export boxes |
Test Liner | Made from recycled paper, cost-effective | General-purpose packaging |
White Top Liner | Kraft liner with a white coating, aesthetic | Retail and display packaging |
Oyster Liner | Mottled appearance, made from mixed paper | Low-cost, non-critical packaging |
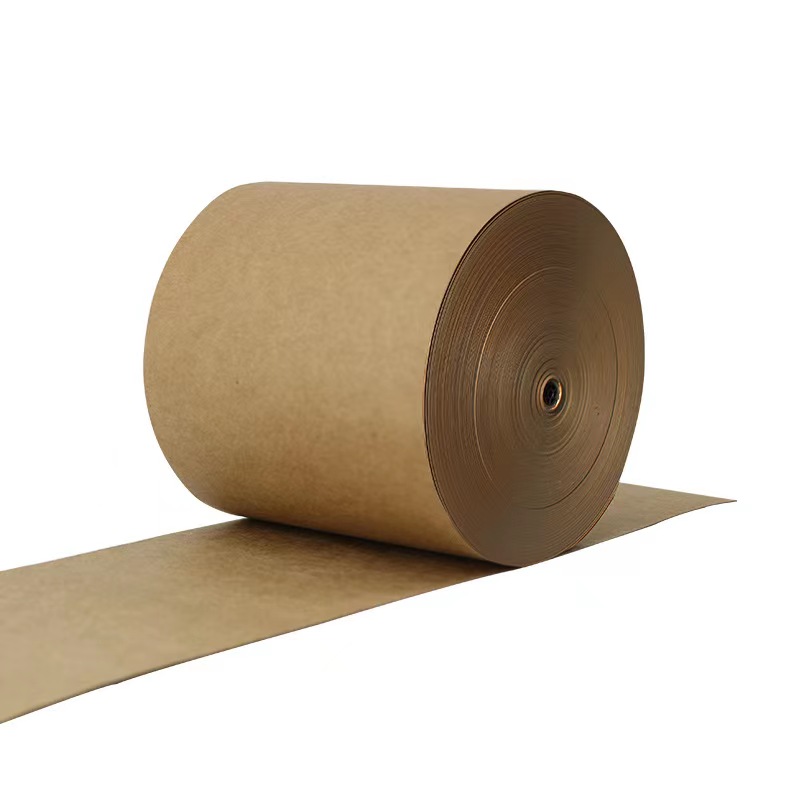
Fluted Medium (Corrugated Layer)
The fluted medium provides cushioning and support. Depending on the flute height and density, corrugated boards are classified as A, B, C, E, and F. Different types of flutes provide different thickness, strength, and levels of cushioning:
Flute Type | Thickness (mm) | Flutes per Meter | Strength | Common Uses |
---|---|---|---|---|
A Flute | 4.5–5.0 | 105–125 | High cushioning | Fragile items, glassware |
B Flute | 2.5–3.0 | 150–185 | Good crush resistance | Canned goods, retail packaging |
C Flute | 3.5–4.0 | 120–145 | Balanced strength | General-purpose shipping boxes |
E Flute | 1.0–1.5 | 290–320 | Thin and lightweight | Pizza boxes, cosmetic packaging |
F Flute | 0.6–0.8 | 400–440 | Ultra-thin, high print quality | Small retail boxes, luxury packaging |
Additionally, they can be combined based on their characteristics to achieve complementary functions. For example, combining to form AB type corrugated board, BC type corrugated board, or AC type corrugated board.
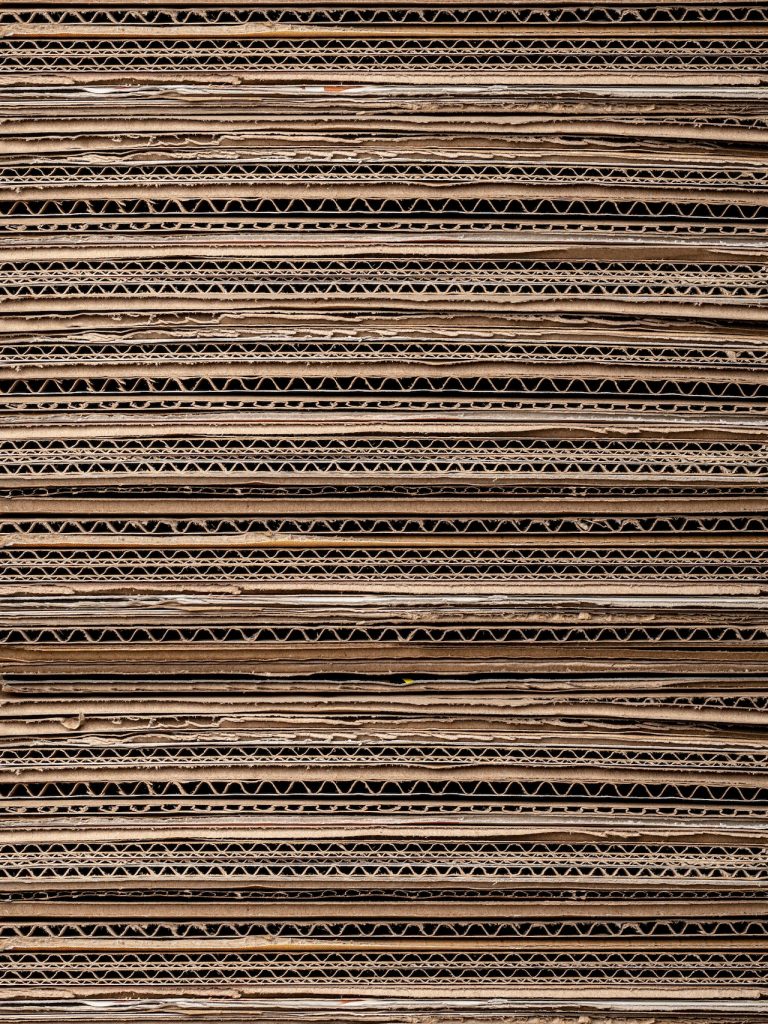
4. Types of Corrugated Boxes
Corrugated boxes are categorized based on the number of fluted layers and their combinations. Each type has unique properties that make it suitable for specific applications. Below, we’ll explore the characteristics of single-wall, double-wall, and triple-wall corrugated boxes, followed by an explanation of how double-wall and triple-wall boxes are made by combining different flute types, and finally, a detailed look at common flute combinations and their characteristics.
Single-Wall, Double-Wall, and Triple-Wall Corrugated Boxes Characteristics
Type | Layers | Thickness (mm) | Bursting Strength (kPa) | Max Load Capacity (kg) | Stacking Limit | Common Uses |
---|---|---|---|---|---|---|
Single-Wall | 1 fluted layer | 3.0–5.0 | 200–400 | 20–30 | 2–3 layers | Lightweight items, retail packaging |
Double-Wall | 2 fluted layers | 6.0–7.0 | 600–800 | 40–60 | 4–5 layers | Heavy items, industrial packaging |
Triple-Wall | 3 fluted layers | 9.0–10.0 | 1000–1200 | 80–100 | 6–8 layers | Extreme durability, machinery |
Single-Wall Boxes: It is the most common and cost-effective type, with a single fluted layer sandwiched between two linerboards. They are lightweight and utilized for general packaging purposes.
Double-Wall Boxes: They have two fluted layers and three linerboards, offering enhanced strength and better cushioning. They find application in packaging heavier items and long-distance shipping.
Triple-Wall Boxes: The strongest type, with three fluted layers and four linerboards, for very heavy or bulky items. They are commonly used in industrial and automotive packaging.
Flute Combination Principles
The combination of flutes in double-wall and triple-wall boxes is not random but follows some principles to optimize performance:
Balancing Cushioning and Strength:
- B flute is often used for its cushioning properties, making it highly suitable to protect fragile items.
- C flute is chosen for its balance of strength and thickness, making it perfect for general-purpose packing.
- E flute is used when high-quality print and a smooth surface are required.
Order of Flutes:
- The order of flutes could impact the box’s performance. For example, in BC flute, the B flute is employed on the outside for better cushioning, and the C flute is employed to add structure.
Common Flute Combinations for Double-Wall and Triple-Wall Boxes
Double-Wall Flute Combinations:
Flute Combination | Thickness (mm) | Bursting Strength (kPa) | Cushioning | Printability | Common Uses |
---|---|---|---|---|---|
BC Flute | 6.0–7.0 | 600–800 | High | Medium | Heavy-duty packaging, furniture |
EB Flute | 4.5–5.5 | 500–700 | Medium | High | Retail packaging, display boxes |
BE Flute | 4.5–5.5 | 500–700 | Medium | High | Lightweight yet sturdy packaging |
EF Flute | 3.5–4.5 | 400–600 | Medium | Very High | High-end retail, cosmetic packaging |
CE Flute | 5.0–6.0 | 550–750 | Medium-High | High | General-purpose, e-commerce |
Triple-Wall Flute Combinations:
Flute Combination | Thickness (mm) | Bursting Strength (kPa) | Cushioning | Printability | Common Uses |
---|---|---|---|---|---|
BCC Flute | 9.0–10.0 | 1000–1200 | Very High | Low | Heavy machinery, automotive parts |
BCB Flute | 9.0–10.0 | 1000–1200 | Very High | Low | Industrial packaging, bulk shipping |
ECC Flute | 8.0–9.0 | 900–1100 | High | Medium | High-end retail, luxury packaging |
BBC Flute | 9.0–10.0 | 950–1150 | Very High | Low | Heavy-duty industrial packaging |
EEB Flute | 7.0–8.0 | 800–1000 | High | High | High-end retail, lightweight heavy-duty packaging |
5. Manufacturing Process
The corrugated box manufacturing process is a multi-stage process, and all the stages are important to achieve the quality and performance of the finished product.
Raw Materials: Corrugated boxes are mostly made of kraft paper (virgin wood pulp) or recycled paper. Over 90% of corrugated boxes in the United States are made from recycled material, according to the Fibre Box Association (FBA).
Manufacturing Steps:
- Corrugating: Fluted form is created by running paper through corrugating rolls.
- Laminating: Bound together with fluted paper sandwiched between linerboards to create corrugated board.
- Cutting and Shaping: Scoring and cutting of board to create box blanks.
- Printing and Finishing: Boxes are printed with designs, logos, and information.
Data Insight: Smithers (2022) research were of the opinion that corrugated packaging market worldwide would increase at 4.2% CAGR during 2022-2027 with growth in technological development in the manufacturing process.

About the printing
Printing on corrugated boxes can be done in two basic ways: pre-printing and direct printing. The term “direct printing” refers to printing directly on the box. Pre-printing is the process of printing outer liner paper first and then combining it with other parts.
In direct printing, flexographic printing, offset printing, and screen printing is commonly used.
- Flexographic printing: In general, flexographic printing lines or printing slotting machines are used to print directly on corrugated board using water-based inks. The printers are suitable for printing large formats and general quality requirements based on text and lines. Because flexographic printing involves light pressure, it has little effect on the strength of the corrugated board, resulting in a stronger finished product
- Direct offset printing: It has the advantage of high printing quality, low printing costs, and short loading and adjustment times; this process can ensure good carton molding and also complete fine outer liner printing.
- Screen printing: although the resolution of the print is not high, the image accuracy is low, the ink color is thick, the color saturation is high, and the visual effect is strong, especially for spot colors
- Digital printing: this method is more suitable for small batches since it is more expensive and takes longer than the above mentioned printing methods when printing large quantities
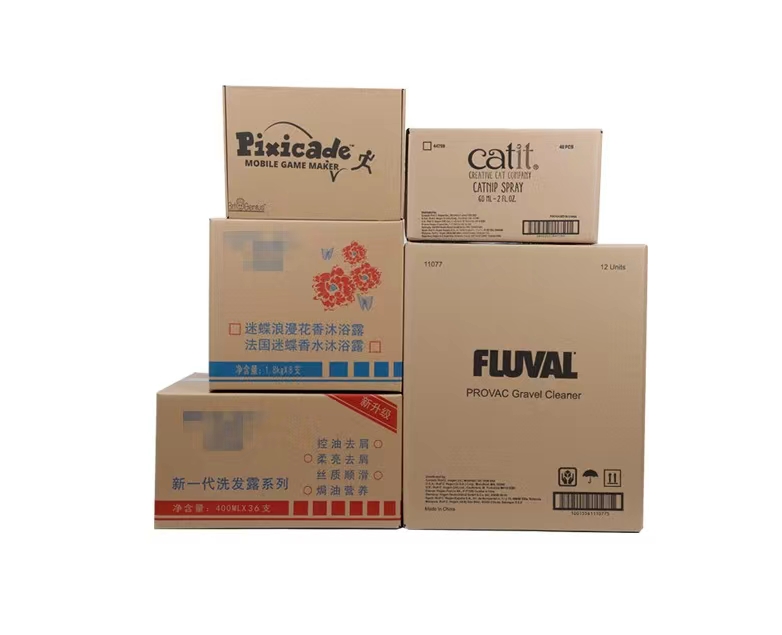
Printing methods commonly used for pre-printing include flexible printing, offset printing, plastic gravure printing, and coated paper gravure printing.
- Flexographic pre-printing: Printing is performed on a whole roll of face paper, followed by finishing on an automated corrugator production line. While the printing quality and forming quality of the box are relatively high, the investment required is substantial, and it is not suitable for small batch production. Furthermore, due to the high temperatures and pressures required when processing the corrugated board after printing, special inks must be used.
- Offset pre-printing: since this technology is extremely popular, boxes for sales with small batches and high-quality requirements are now commonly printed indirectly by offset printing, i.e., the outer liner is printed first, and then the printed liner is laminated to the corrugated board. Corrugator linkage production lines are not suitable for this process, but only single facer corrugators, which have low production efficiency. In addition, the printing width is limited and the printing costs are high.
- Plastic gravure printing: If you still need to laminate after your liner printing is completed and the production batch is larger, gravure printing can be used to print on plastic film with a white background, then laminate the printed plastic film with the outer liner, and then complete the box making process according to conventional box forming procedures. Its printing effect can be compared to that of offset printing. When the production batch is larger, this process can greatly reduce the printing and material costs of the outer liner.
- Coated paper gravure printing: The process can be used when the production batch is relatively large, does not require lamination, and requires a good printing effect at a reasonable cost. First, gravure printing is used to print thinner coated paper, which is then laminated with the original outer liner, resulting in a new outer liner that is then formed into a box as usual.
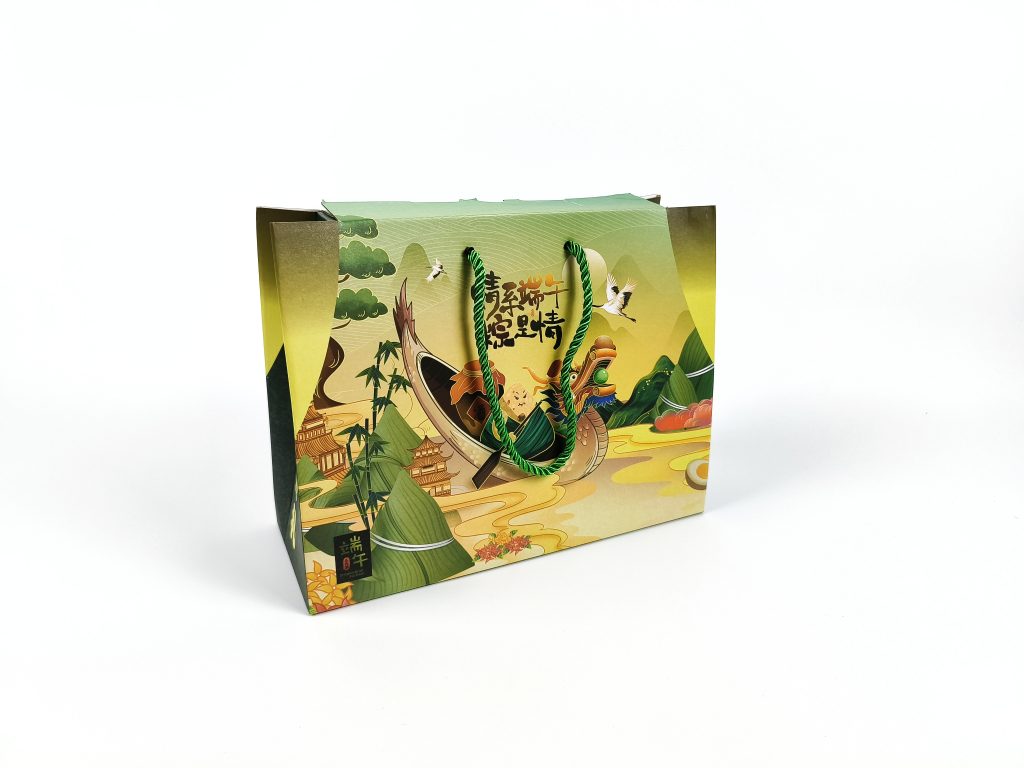
6. How to test the quality of corrugated boxes
The most common performance tests for cartons are edge crush tests, folding endurance tests, bursting strength tests, puncture resistance tests, and compression strength tests.
- Edge crush tests: a certain width of the corrugated board is tested to determine the maximum pressure it can withstand per unit length parallel to the flute direction. Using this test, you can determine the flute strength inside the corrugated box, which directly affects the strength of the corrugated box. In a corrugated box, gravity is primarily supported by the flutes inside, and side pressure is one of the best methods of assessing the flute’s strength.
- Folding endurance tests: It is using a sample corrugated board of 150mm x 15mm specifications, for a reciprocal folding test at a 135° angle, when the paper breaks, that is, the number of folding resistance tests.
- Bursting strength tests: Refer to test the maximum pressure perpendicular to the surface that the corrugated board can withstand per unit area. In this test, the box will be tested for its ability to withstand static local extrusion in an actual transportation environment. This test can be used to understand the ability of the box to withstand the handling, loading, and unloading, impact and tearing forces in the process of circulation, and the breakage resistance of corrugated board is determined by the strength of the liner used and does not depend on the strength of the flute in the middle.
- Puncture resistance tests: using a certain shape of angle cone, this test measures the force required to pierce the corrugated board, expressed in joules (J). Check its resistance to external sudden impacts. It is designed to provide a simulation of the impact force of a box during use or transportation. In this test, corrugated board is evaluated for its ability to withstand the impact of sharp objects. Puncture resistance strength is closely related to its fiber toughness, hardness, tightness, and moisture content, as well as its glue strength and thickness.
- Compression strength tests: The objective is to determine the maximum pressure that an empty corrugated box can withstand when it is placed normally and pressed at a constant rate on both sides. In this test, the box is evaluated for its ability to withstand a sufficient amount of stacking weight and whether it can protect its goods from deformation, damage, and other undesirable phenomena caused by inadequate strength during use, handling, stacking, storage, and transportation of the product, as well as a comprehensive reflection of the box’s protection performance.
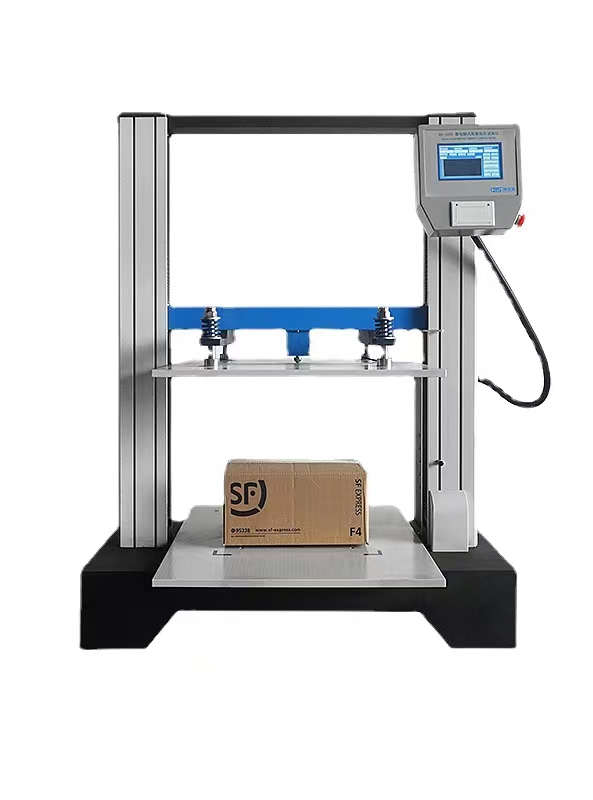
7. Benefits of Corrugated Boxes
There are a number of benefits of corrugated boxes:
- Strength and Rigidity: Fluted construction has excellent resistance against impact and compression loads.
- Light Weight: The corrugated boxes are light in weight, which reduces the shipping weight as well as expenses.
- Low Expense: They are inexpensive to make and can quickly be customized in any shape as desired.
- Environmentally Friendly: Corrugated boxes are recyclable and biodegradable. In Europe, 89% of corrugated packaging is recycled, reports the European Federation of Corrugated Board Manufacturers (FEFCO).
- Recyclability: Corrugated boxes can be recycled seven times without loss of quality. Paper and Paperboard Packaging Environmental Council (PPEC) claims North American recycling levels for corrugated containers at over 90%.
- Biodegradability: Unlike plastic, corrugated boxes biodegrade, occupying less landfill space.
- Innovations: Businesses are creating lightweights and using water-based inks in an attempt to reduce environmental impact even further.
Comparison with Other Packaging Materials
Here’s a detailed comparison of corrugated boxes with other packaging materials:
Material | Strength | Weight | Cost | Eco-Friendliness | Common Uses |
---|---|---|---|---|---|
Corrugated | High | Light | Low | Highly recyclable | Shipping, retail, food packaging |
Plastic | Medium | Light | Medium | Low recyclability | Bottles, containers, bags |
Wood | Very High | Heavy | High | Biodegradable | Heavy machinery, pallets |
Foam | Low | Light | Medium | Non-recyclable | Fragile items, electronics |
8. Conclusion
Corrugated boxes are the backbone of modern packaging, and they offer a perfect combination of strength, flexibility, and environmental friendliness. From their inception to their current status in global commerce, these boxes have never been replaced. With technology becoming more advanced and environmental concerns mounting, the future of corrugated packaging is brighter than ever.
Frequently Asked Questions (FAQs)
Q: How Much Weight Can a Corrugated Box Hold?
A: Single-wall corrugated Boxes max load 20–30 kg (44–66 lbs), Double-wall Corrugated Boxes max load 40–60 kg (88–132 lbs), Triple-wall Corrugated Boxes max load 80–100 kg (176–220 lbs).
Q: Can Corrugated Boxes Be Used for Food Packaging?
A: Yes, corrugated boxes are being used commonly for food packaging. They are safe, hygienic, and can be provided with food-grade liners for additional protection.
Q: What Is the Difference Between Edge Crush Test (ECT) and Bursting Strength?
A: Bursting Strength measures the force required to rupture the box material. It is expressed in kilopascals (kPa). Edge Crush Test (ECT) measures the box’s stacking strength by applying pressure to its edges. It is expressed in pounds per inch (lb/in). Example: A box with a bursting strength of 600 kPa and an ECT of 32 lb/in is suitable for heavy-duty packaging.
Q: Are corrugated boxes recyclable?
A: Yes, they are highly recyclable and biodegradable.
Q: What Are the Trends in Corrugated Packaging?
A: Smart Packaging: QR codes, RFID tags, and augmented reality integrated into packaging. Sustainability: Increased use of lightweight structures, water inks, and bio-adhesives. E-Commerce Growth: Rising need for durable and personalized boxes for shipping via the internet.
References
- Fibre Box Association (FBA). (2023). Corrugated Packaging Industry Overview. Link
- Smithers. (2022). The Future of Corrugated Packaging to 2027. Link
- European Federation of Corrugated Board Manufacturers (FEFCO). (2022). Recycling Rates for Corrugated Packaging in Europe. Link
- Paper and Paperboard Packaging Environmental Council (PPEC). (2023). Recycling Rates in North America. Link